Northwestern mineralogist leads lunar soil analysis for NASA’s MMPACT project
Most people are familiar with the iconic photograph of astronaut Buzz Aldrin’s boot print on the surface of the moon. But what, exactly, is in the soil that holds the imprint of that famously “small step for man”?
The answer to this question is more than a fleeting curiosity — it’s essential knowledge for NASA’s Artemis program, which aims to build a permanent base on the moon. While researchers understand the general makeup of the lunar soil, Northwestern University mineralogist Steven Jacobsen has received funding from NASA’s Marshall Space Flight Center to further unravel the mystery of the dubious dust.
Because the cost of bringing traditional building materials from Earth is incredibly high, NASA has partnered with robotics and artificial intelligence company ICON Technology Inc. to explore new methods for building a lunar outpost using the moon’s own resources. But before ICON can build structures with the moon’s soil, the team first needs to understand the soil’s exact composition, which can change drastically from one sample to the next.
To characterize these samples, Jacobsen is working closely with his former student Katie Koube, now a materials scientist at ICON, to analyze various samples using Northwestern’s facilities. Their end goal is to create a library of potential sample compositions, which will be used to optimize parameters for the building process.
“Off-world construction comes with many challenges,” said Jacobsen, the project’s principal investigator. “The moon’s soil is not like that on Earth. On the moon, soil is formed from meteoroid impacts that have crushed the surface. So, the moon is essentially coated in a thick layer of pulverized flour. The types of minerals and glass found in lunar soil depend on many factors. The material can vary widely within even a small area.”
Jacobsen is a professor of Earth and planetary sciences at Northwestern’s Weinberg College of Arts and Sciences. He also is a faculty affiliate with the Paula M. Trienens Institute for Sustainability and Energy and the Center for Engineering Sustainability and Resilience. Members of the project also include Laura Gardner and Tirzah Abbott, who are Ph.D. candidates in Jacobsen’s lab.
The dangers of dust
With plans to travel back and forth to the moon more regularly, NASA first needs a reliable landing pad. Otherwise, every time a lunar lander makes contact with the moon’s surface, it will kick up destructive dust that could gum up equipment and damage the surrounding habitat.
“Each particle of dust on the moon is jagged and angular,” Koube said. “When you think of grains of sand on Earth, they are rounded because weathering removes all those rough edges. Without weathering, the particles remain bumpy and sharp. So, if a rocket lands directly on the moon’s surface, it stirs up abrasive dust that basically sandblasts the whole area.”
In November 2022, NASA selected ICON for a $57.2 million grant to develop lunar construction technology. The contract builds upon previous NASA and Department of Defense funding for ICON’s Project Olympus to research and develop space-based construction systems to support planned exploration of the moon and beyond. ICON’s Olympus system is intended to be a multipurpose construction system primarily using local lunar and Martian resources as building materials to further the efforts of NASA as well as commercial organizations to establish a sustained lunar presence. ICON is already using its advanced 3D-printing technology to build homes on Earth. By putting multipurpose in situ resource utilization (ISRU)-based lunar construction systems on the moon, the team aims to use lunar resources as the building blocks for construction.
“It’s not feasible to send traditional Earth-based construction equipment and materials to the moon,” Jacobsen said. “The payload would be too heavy. So, this plan is a lot more practical. Just as the first bricks on Earth were made out of terrestrial soil, the first bricks on the moon will be made out of lunar soil.”
Simulated soil samples
After ICON received NASA’s funding, Koube, who graduated with a dual degree from Northwestern’s materials science and Earth and planetary sciences programs in 2014, contacted Jacobsen to lead sample analysis. The pair assembled a team that works with NASA’s Marshall Space Flight Center in Huntsville, Alabama, under the Space Technology Mission Directorate’s Moon to Mars Planetary Autonomous Construction Technologies (MMPACT) project.
At Northwestern, analysis is already underway. Gardner and Abbott currently are using various microscopy techniques to analyze eight lunar simulants — faux moon soil that is designed to mimic the real thing — and synthetic plagioclase, a brittle, greyish-white mineral that is a major constituent of moon rock. Then, the team will compare the lunar simulants to actual samples collected from the Apollo missions.
“Of course, we know from Apollo missions what’s in lunar dirt — and that it’s very heterogenous (or variable),” Jacobsen said. “Our job is to anticipate the likely variability in lunar soil and come up with a way to measure it on the fly, onboard the 3D printer.”
So far, the researchers have noticed vast differences among the lunar simulants. In some minerals, the team has detected hydrogen — a component of water, which is not abundant in minerals on the moon. They also are on the lookout for mineral impurities in the simulants that are not expected on the lunar surface. The team can then focus on materials and chemical variations that the construction processes are more likely to encounter.
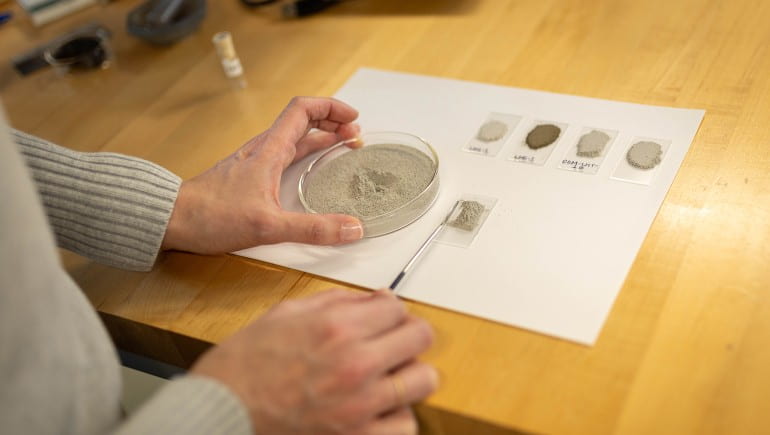
Various samples of lunar soil simulants in Steven Jacobsen’s laboratory. Photo by Shane Collins
No scoop is the same
After determining variability in realistic samples, the researchers will probe how the composition of dirt can affect the melting process used in robotic construction. Once on the moon, ICON’s multi-purpose ISRU-based lunar construction systems will scoop up lunar soil and melt it for printing. After printing, the melted dirt will harden and cool into a ceramic material.
“On Earth, you can gather clay and fire it in a kiln to make ceramics,” Jacobsen said. “But the properties of lunar soil are such that it needs to be melted first. Different minerals in lunar dirt melt at different rates, so the 3D-printing process is very sensitive to changes in mineralogy.”
And, of course, no sample is the same. One scoop of lunar dirt might have a different melting point than the next scoop. The 3D-printing technology needs to be nimble enough to know how to handle these subtle differences. That’s where Jacobsen’s sample library comes into play. By enabling the 3D printer to be prepared for all potential compositions, it can perform diagnostics of each scoop and then adjust its laser parameters for heating and cooling.
“Without understanding the characteristics of the soil, it’s difficult to understand the variability of the final printed materials,” Jacobsen said. “Using the library that we create from simulants — cross-checked against the lunar soil — the printer will know how to process each piece to produce the best ceramic. That detailed library of information will play a part in making the imagined outpost a reality.”